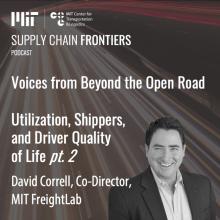
Earlier this year, MIT CTL's David Correll spoke with over-the-road truckers about their experiences in order to shed light on why it is that U.S. truckers appear to be both scarce and underutilized at the same time.
During the year, Dr. Correll oversaw three MIT SCM master's capstones that addressed truck driver utilization and retention in contrast to shipper and receiver policies and practices. These were completed as part of the MIT FreightLab's Driver Initiative.
In today's episode, we hear how a variety of factors influence driver utilization, and how they may impact the widespread driver shortage currently experienced in the U.S. David's guests offer solutions that shippers, warehouse managers, dispatchers, and their companies can implement to improve.
Read the capstones covered in this episode.
Diving Deep into the Determinants of Driver Dwell Authored by: Michelle Catherine Roy, Leora Reyhan Sauter
Goldilocks and the Three Dispatchers: Quantifying the Impact of Dispatcher Management on Truck Driver Performance Authored by: Danielle Procter, Paulo Sousa Jr.
Automation of Warehouse Decision Making Authored by: Roogers Marino, Zeyu Wu
Transcript
Narrator:
Welcome to MIT Supply Chain Frontiers from the MIT Center for Transportation and Logistics. Each episode features center researchers and staff who welcome experts from the field for in-depth conversations about business, education, and beyond. Today, David Correll reflects on what we heard in February speaking with truck drivers on our Voices of the Open Road episode. He compares these driver stories with findings from three of the MIT supply chain management master's thesis projects relating to the complexity of America's freight trucking networks. Take it away, Dave.
David Correll:
Early in the year, as part of the MIT FreightLab Driver Initiative, we talked with three working American truck drivers about their experiences in trucking. We asked them what shippers and receivers could do to help or hurt their utilization and ultimately their take home pay. Because when we consider the driver shortage problem in the US, people often think that it's something that drivers are doing or not doing that could fix the shortages within over the road transportation, or perhaps help reign in the currently high costs, but our conversations and our research is indicating that while it is within this sphere of concern of drivers to increase their utilization and decrease their dwell time, it is perhaps only within the sphere of influence of the shippers and the carriers they service to actually make the changes that could make these improvements. When we spoke with over-the-road truck driver, Mark Cavanagh, back in March, he shared a simple version of how shippers can help improve drivers' lives.
Mark Cavanagh:
Yeah. When you show up on time for your appointment or even early, and they get you right to a door within two hours, they've given you a green light and given your paperwork and you're back out again. I mean, that's perfect. That's my ideal customer service.
David Correll:
Instead of looking at what drivers themselves control inside the cab, we began to look at how the institution's drivers work with control their experiences of dwell and utilization from outside of the cab.
Desiree Wood:
A good experience for me is when you arrive and they're ready for you and they have a door for you and they have a bathroom for you to use and a clean driver lounge, where you can have a seat or microwave something and get some snacks out of the machine if you need to. Treat you with respect, a lot of them don't.
David Correll:
Desiree Wood known to many people as Trucker Desiree.
Desiree Wood:
And if you're out of hours, having a small area that you could park the truck and do your 10 hour break. You go someplace like that and you're like, oh, at least I'll come here again.
David Correll:
We're also joined by Paul Marhoefer known to many of his adoring fans as Long Haul Paul.
Paul Marhoefer:
I'll tell you about the greatest food warehouse I've ever been to, it was 14 years ago. It was Sysco Foods in Alachua, Florida, and whoever designed and implemented that warehouse was to food warehouses and trucking what Temple Grandin is to cows and slaughterhouses. Got there, you checked in with the guard. He said, at three o'clock in the morning, I'm going to call you and we'll assign you with a door. Boom, three o'clock in the morning, here comes your call. They put you in a door and by the time you could even use the restroom, you're empty. The person who designed that should be canonized. There should be votive candles of that individual for sale on every truck stop. So truckers like me could light a votive candle and quietly meditate by it.
David Correll:
One thing that a researcher can do is to take a look from an outsider's perspective. We are no way really experts at the industries that we study because we don't do the actual work. We don't really play the game. Instead, we are more like commentators. People who watch the game from a distance, looking for fresh or interesting perspectives and insights. And in my world that typically means data, lots and lots of data. This is a story in two parts. One, what we've learned about what trucking companies can do to improve drivers utilization and retention. And two, what shippers and receivers can do to reduce waiting time at their facilities. I'd like to introduce you to the members of the graduate student teams who worked with me this past year to follow up on what the drivers told us this spring. First, please meet my friends, Leora and Michelle who studied unplanned downtime and recently graduated from the MIT SCM Masters in supply chain management.
Leora Sauter:
So, hi, my name's Leora Sauter. I graduated from West Point in 2015 and spent five years in the active duty army as a logistics officer, finished out my military service last summer and joined my class here at MIT. Very thankful to be graduating here shortly.
Michelle Roy:
Hey everybody, I'm Michelle Roy. I graduated with my undergrad in supply chain management from Texas A&M in 2016, and then spent several years doing procurement in the oil and gas industry before I joined the SCM class of 2021.
David Correll:
How would you explain what you studied for your capstone project?
Leora Sauter:
So I guess to give a bit of background, a daily shift for a driver is 11 hours, driving hours within a 14 hour total work day but our sponsor company found that their drivers were averaging about six and a half hours driving time per day, which is pretty consistent across the industry. And that's due to various sources of driver dwell. And we define dwell in this context as unplanned unproductive downtime, while drivers are on the clock.
Michelle Roy:
So we were looking to really understand where unplanned downtime comes from in a driver's schedule and day to day activities. We looked at four main hypotheses to understand where this could be coming from. So whether that had to do with the geography of the node they were visiting, what time of day they arrived to their appointment, whether it was drop and hook or live load. So kind of that element of how many hands are in the pie of when they make a drop-off or pickup. And then we also looked at driver demographics. So does age play a role? Does months of experience play a role and does gender play a role? And then finally we considered, do repeated visits to the same node by a driver, does that have an impact on how much dwell they experienced.
David Correll:
Now that we understand what motivated your study? How did you research those questions? How did you conduct your study?
Leora Sauter:
So I'll start kind of broadly talking about why we focused on what we did, and then maybe Michelle can talk about kind of our quantitative and qualitative methods. But before that, just talking about measuring utilization. So utilization is a ratio of actual use to maximum capacity. So for truck drivers, this is hours driven over 11, and that's why we really focused on hours of service as our metric here. Talking to different players in the trucking space, we learned that some companies use things like dollars per week or miles per week, but these address productivity more than they do utilization.
Michelle Roy:
We were fortunate to be given a really big dataset from our sponsor company that gave us a lot of opportunity, both TMS information, so transportation management system information and ELD data. So that comes from the electronic logging devices that drivers use that give us information about where they are, what their status is and other details like that. We'd had to define dwell within those datasets and so for the TMS data, we defined it based on the duration of their visit to a node. So what we did there is we took is this a drop and hook or live load? If it's drop and hook, the expectation is that it takes 45 minutes. If it's live load or unload, the expectation is that it takes two hours. And so that's what we compared to to calculate our dwell within the dataset, as we had the arrival time of the driver, and then the time that they left the facility. And so was that beyond the expectation, depending on whether it was live load or drop and hook.
Michelle Roy:
So that's how we calculated dwell for that dataset. And then for the ELD dataset, where we focused more on the drivers themselves and the demographics, we used their time in on-duty status, which basically means that they're using their hours of service, but they're not actually driving. So it's not really productive time for them or for their company. With that in mind, we did some regression testing against our, with the context of our hypotheses to understand are these factors significant contributors to the dwell that we're seeing. So could we say for example, that as somebody's number of visits to the same node increases that their dwell time proportionally decreases and that's the kind of relationships that we were looking for when we did this hypothesis testing.
Michelle Roy:
The other side of the testing that we did or the research that we did here was more qualitative in nature. And we had the opportunity at our sponsor company to talk to really a broad array of people that helps paint a picture for us of what does it look like to be a truck driver today and what really makes up that landscape? So we were able to talk to some people more in senior leadership, and then also we were able to talk to a few drivers and hear from them what's it like to actually be on the road?
Michelle Roy:
So the really cool thing about the timing is that we had some of those higher level conversations first leading into our quantitative research and testing and then after we had some initial conclusions from the quantitative testing and the regression analysis, we went back to the drivers and were really able through asking some broad questions about their experiences, we're really excited to see that there was a match between what we were finding in the data and what their experiences were just really anecdotally describing their day to day and what happens if you're late.
David Correll:
Excellent. What did you find?
Michelle Roy:
I would say we have three big takeaways. The first one is about driver demographics that we found that there really is not a perfect driver demographic when it comes to dwell that they experience. And so the dwell that a driver experiences is not a reflection of their age or their months of experience or their gender and that leads me to parts two and three of what I think are the most interesting things we found were that dwell really is more in the control of the people that support drivers in their jobs.
Michelle Roy:
So dispatchers and people working at the nodes, as far as dispatchers go, what they can relate to is send drivers to nodes during peak hours of activity and this may seem counterintuitive, but what the numbers show is that when you are a driver and you show up during those peak hours, which we defined as between 7:00 AM and 5:00 PM, you're getting in and out of a node a lot faster than if you show up during off peak times. Then the final thing that we found is that drivers who make repeated visits to nodes do see a decrease in their overall time spent at the node.
Leora Sauter:
In one of our hypotheses, we did find that repeated visits to the same node decreases dwell at that node, we use the TMS data and we counted the distinct number of orders between a driver and a node and used that count as a proxy for the number of visits. What was really interesting is that in over 90% of the data, at least from our company, those driver location pairs were either one or two. So in simpler terms, that means that the vast majority of the time, more than 90% of the time, at least in the six month period that we were exploring, these drivers at our company are only visiting the same location once or twice. So we really think that that's a big area where the company could focus and that there's a big opportunity there too.
Michelle Roy:
I mean, it makes sense for probably any of us to say if you move to a new town and then go to a new grocery store, it's probably going to take you longer in that first trip to a new grocery store to understand what the layout is. And then for subsequent visits your time in and out is going to get a lot faster because you know where things are. And so really that same principle can be applied to our truck drivers and repeated visits to nodes that just in a very human way, they understand where do I check in? Who do I talk to? And that really decreases the dwell that they experience at those nodes and the total time that they're at those nodes. So for me, those are our biggest, most interesting findings.
David Correll:
So, so many people right now are thinking about driver dwell. What do you think people might not yet understand about the causes or the solutions to the driver dwell problem?
Leora Sauter:
When Michelle and I were first assigned to this project, I fully expected that driver dwell would come from things that drivers were or weren't doing or would come from some characteristics of the drivers themselves. But through the course of our project, as Michelle mentioned, we really learned that it's really the people around the drivers, both their own dispatchers and then perhaps staff at the shipper and receiver facilities that have the most impact on driver's dwell. And I think for trucking companies maybe they don't have a lot of control over those shipper and receiver facility staff, but they certainly do have control over their own dispatchers. So sharing our findings about sending drivers to nodes during peak node activity times and sending drivers to the same nodes over and over again, those are totally things that are in the company's control and things that they can share with their dispatchers.
Michelle Roy:
I agree. The name driver dwell is almost a misnomer because I think it leads to the idea that it's something that drivers are doing or not doing that's causing this unplanned downtime or underutilization but that really is the core of what we found is that drivers themselves don't have the power to change their own utilization. We can look at drivers collectively really based on our study as a group of people that want to be out on the road, driving and making money and being productive. And so it really is incumbent upon the companies that they work for and the nodes that they visit to help them in that endeavor, because it's not really something that they are equipped to do by themselves, just because of the structure within which they're working through no fault of their own. This really goes back to that same idea of driver dwell is not the fault of a driver and it has nothing to do with their age or gender or months of experience.
Michelle Roy:
And I love that idea because I think we've talked about that there are some people that may feel interested in being a truck driver and that companies should take that interest seriously across the board and really pursue whoever would like to be a truck driver especially obviously through the context of dwell that just because somebody is maybe older has more experience or any of those factors doesn't mean that they're going to perform better in this space. And so I think to me, at least to a degree, this levels the playing field a little bit, so really kind of equal opportunity here and equal opportunity for the companies and the nodes to better serve the drivers that visit them.
David Correll:
So a takeaway here for me was what Michelle said about how much is outside of the driver's control when we look to reduce dwell time. Okay then, who else has influence? What if we look even one step closer into a trucking company's organizational chart? What if we talk about the dispatchers? Please meet my friends, Danny and Paulo who happened to study just that in their paper, Goldilocks and the Three Dispatchers.
Danielle Procter:
Hello, my name is Danielle Procter.
Paulo Sousa Jr:
Hello, I'm Paulo.
David Correll:
In the simplest terms, what did you study in your capstone project?
Danielle Procter:
What we looked at is freight truck drivers in the US, which we all know and love from highways and from getting all of our things. And we looked at what has the greatest impact on their performance measured in a couple of different ways. And really where we focused in was what we felt was the understudied impact of carrier dispatchers. So the people that aren't on the road with the truckers, but are actually back home with the carriers, assigning loads to the truckers, telling them where to go, how to get there and what's next.
Paulo Sousa Jr:
We were looking for somehow to improve truck driver utilization in the United States. We wanted to provide some insightful recommendations for management.
David Correll:
Now maybe with a little bit more detail, how did you do it? We know what you wanted to study. How did you approach this question?
Danielle Procter:
What we had access to was six months of data about truckers. We partnered with a mid-size Midwestern freight carrier, and they gave us information from the electronic logging data. So this is information captured by the computers on board of the trucks themselves. So it captures what the truckers were doing at every hour of the day while they were working, their transportation management data. So that captured sort of what the freight loads were and who the dispatchers were that assigned them and then some employment and tenure data on the truck drivers. And we used that to do some data analytics and some machine learning to find what were the features that most impacted truck driver performance and what of those came from the carrier organization or from the dispatchers themselves.
David Correll:
Excellent. Thank you. Paulo, same question and maybe if it's more comfortable to focus on some of the analytic tools you applied.
Paulo Sousa Jr:
Sure. We have investigated both a traditional method and a more sophisticated method. We use linear regression to investigate some features that impacted on utilization and efficiency, but we also have used some unsupervised machine learning techniques to cluster dispatchers. What we really wanted is to find if there are some common patterns between the ... that can deliver more expected results for the company, and we have clustered them to identify these common features among those.
David Correll:
Excellent. Thank you. And what did you find?
Paulo Sousa Jr:
I would say that we have three key takeaways. First is that drivers working fewer Mondays, they show higher efficiency according to this dataset. Teams with less evenly distributed plans show higher productivity and this is related to what the dispatcher can do. And third, contrary to our first assumptions drivers on larger teams, they tend to be able to achieve higher efficiency and hour utilization.
Danielle Procter:
So I think the first idea of weekdays mattering, so we found that when drivers drove fewer Mondays, they actually had higher mile per day efficiency. And it's sort of long been anecdotally understood in the industry that Mondays are challenging days for drivers because they're leaving home. Challenging days for dispatchers to assign loads to those drivers, but that Mondays are crucial to carry your productivity and what we actually found is the opposite. And so this is not to say that carriers should avoid assigning loads on Mondays, but I think you don't have to. We don't need to think that a trucker's week is the same as an office workers week. They are different and that perhaps greater flexibility in those schedules or greater understanding in the differences in those priorities of drivers can help carriers better assign their loads. When we talk about the unequality of distribution of freight plans, which is quite the mouthful, but what I think that really means is that it's not necessary to treat your drivers all exactly the same in order to have a cohesive and efficient team.
Danielle Procter:
You can assign loads and miles and trips based on driver interest, based on driver availability, based on some of these different driver profiles and still see really successful driving teams overall. And perhaps one of the most interesting pieces is this idea that drivers actually do better on larger teams. This has two interesting pieces. One is that we found that this performance or these larger teams are highly correlated to greater disparity in this distribution of freight plans. So dispatchers with larger teams actually have more pieces to move around the board to do some of that work that I was just saying, to assign plans based on driver needs, but also it means the carriers don't need to focus on sort of lowering that driver to dispatcher ratio. They can instead focus on maybe hiring fewer dispatchers capable of making more sophisticated decisions and making sure that those dispatchers are really empowered to make the right decision for their driving teams and not worry so much about just getting more of them.
David Correll:
Oh, excellent. Thank you. So many people right now are thinking about the underutilization of American truck drivers and I know that you all have thought about that too. What did you learn about driver utilization or underutilization by looking at this data that could inform the national conversation about truck driver utilization?
Danielle Procter:
Definitely the most surprising and one of the biggest takeaways for us was that there was this trade-off in the metrics that we looked at and the big trade-off was between what I'm sort of summarizing as productivity, so hour utilization and then miles driven efficiency and retention. And so really when we clustered the dispatchers, we saw these three distinct classes and the ones that had the highest retention had the lowest productivity in their drivers and vice versa. And I think that for a long time, there's sort of been this focus on retention because everyone's a little bit freaking out about this idea of a driver shortage. And I think it's possible that we might be thinking about the driver shortage in maybe not the wrong way, but there are other ways to think about it. So when we talk about the driver shortage, we talk about 60,000 drivers short today, we talk about 160,000 drivers short by 2028. That's terrifying, that's alarming. We're not going anywhere. We're not going to need fewer drivers. We're going to need more. What do we do?
Danielle Procter:
And I think, Dave, what your work has done when you look at hour utilization is that perhaps when we talk about the driver shortage, we shouldn't be talking about physical drivers short. We should be talking about available driver hours short. And in that case, maybe retention isn't the most important metric anymore, or perhaps there's sort of a different way of thinking about it. And when we looked at the trade-off between retention and productivity, sort of when I think about it, I think what does this mean for carriers? And it could be that retention isn't sort of the one key, the one sort of silver bullet there's other metrics that we need to focus on. And we can focus on things like hour utilization and improving that, accepting that that might bring our retention levels down a little bit but knowing that we're getting better utilization from our drivers while we have them. And that that might be sort of an alternative solution to this impending driver shortage issue.
Paulo Sousa Jr:
Yeah. I would just say that our study indeed verified that through our dataset, that they are underutilized. They drive around 6.5 hours per day when they could drive 11 hours. And well, we have found a trade-off between retention and hour utilization. So maybe dispatchers or companies may be willing to worry less about retention and to focus more about how to improve their truck drivers' utilization as well.
David Correll:
Excellent. Thank you both. I came up with a hard question, so if you don't have an answer, say we don't have an answer, but if you have an answer, I'd be curious. So say we get some people who are managing trucking firms listening and they hear you and they push back and they say, I don't think so. I think the people that work for me want to make money, and I don't think there's a trade-off I think utilization and retention go together. Drivers that drive more stay with me because they make more money. To me that seems counter to what you all found and how would you convince that listener that the trade-off you identified is accurate?
Danielle Procter:
I'm going to convince them using the most convincing thing that I can say, which is that you're totally right. You're right. You're absolutely right. Yes. So we found these different classes of dispatchers, and we found this trade off, but we also found that there was a dispatcher class that found the balance. There was high retention and relatively high productivity. It wasn't the highest retention and it wasn't the highest productivity, but it did sort of find that maybe perfect balancing point between the two.
Danielle Procter:
I would say truckers are like anyone else, they're willing to work harder to make more money but at some point you hit a limit. At some point, the trade-off isn't there anymore. And especially when you're talking about a group of people who are as a rule, older and have families, there is going to be a point where it's not worth that one more load. It's not worth that one more trip even though it's worth more money, they want to go home. They want to take a break. They want to see their families. And so, yes, if you want to keep truckers happy, you have to pay them money. Everybody wants to make money, but you can overshoot it.
Paulo Sousa Jr:
Yeah. I agree with Danielle, there should be a limit for everyone, right? You want money? You want to work, but yeah, everyone has life and other objectives, maybe other things to solve and to leave for as well. I'll also say that maybe we don't need to think a driver as a standard driver, we have different drivers, different ages. So maybe some drivers that are more younger, they are more willing to spend more time out of their homes but those who already have established family or another context, maybe they are not willing to spend so much time out of their homes. So we should realize that there are different drivers as well.
David Correll:
Imagine now that it's the end of a workday and you've been to work and they have to go to the grocery store and now you're pushing the cart. That one cart with the one infuriating wobbly wheel back to your car in the parking lot. You just want to get home. As Paulo put it, you have other things to solve for and other things to live for. Truckers are just like anyone else. We can push them too hard. Take them too far away from the other things that they have to solve for and to live for. I think we do that far too often because we don't manage our dispatching to meet their needs. If we've looked at what trucking companies can do, how can warehouse staff get better? Maybe we can't all achieve that sainted status that Long Haul Paul brought up at the top of the hour, but maybe we can all change our practices even just a little bit in order to do incrementally better. Please meet my friends, Zeyu and Roger.
Zeyu Wu:
Hi, my name is Zeyu Wu.
Roger Marino:
Hi. My name is Roger Marino.
David Correll:
In the simplest terms, what did you study in your master's capstone project?
Zeyu Wu:
We started automation of warehouse decision-making.
Roger Marino:
We tried to eliminate the human decision factor in the decisions for the warehouse. So our study focused on the inbound side of the warehouse. It's from the data we received. It's where we saw the biggest opportunity for improvement. So here it's where the trucks arrive to the warehouse and then they're either assigned to a dock door or they have to wait at the drop-off, which is a parking space. And they wait there until there's labor and space available. And from what we saw the trucks were waiting there for a long period of time. And our goal was to reduce this waiting time until they were unloaded.
Zeyu Wu:
In our modeling, the company's situation when their trucks entering the bay, a checking time will be logged and the inbound coordinators need to prioritize while there's manual ID or why this shipment that content's short. If there is any dock available, they will send these to prioritize the shipment first to the available dock. Otherwise, the trucks will form a waiting queue at the drop-off. And once the trailer moves to the dock for unloading, the warehouse coordinator will assess, assign a special counterbalance forklift and forklift driver to unload the truck and then once the process finishes the truck can leave the dock. Even simulation model by, this model contains several decisions and we use several distributions to simulate the reality and generate the variables. We use this model to test different scenarios and policy combinations to find out the best policy for different scenarios.
Roger Marino:
So for our simulation model, what we did, we created a scenario that we checked with the company to confirm that our numbers were correct. And once we had our baseline model, we created different scenarios and each scenario changed the truck arrival distribution. So in our first scenario, the trucks arrive normally. On the second one, we had little spikes, it was a little lumpy, the distribution. And for the third scenario, it was a quarterly push. This means that at the end of every quarter, there's increased demand. So more trailers arrive to the facility. And through these three scenarios, we tested different unloading policies. The first one was treating a certain type of truck called manual IDs. We would unload them at the end with the lowest priority. The second policy would treat them with the highest priority meaning they would be unloaded first. The third policy treated these trucks like any other truck and we proceeded to unload them with a FIFO model, which is first in, first out. And the final policy designated a special dock and special labor only for these certain types of trucks.
Zeyu Wu:
When we use the simulation model to simulate the different scenarios we use, we call it a drop-off waiting time, but it's actually the time intervals between the truck check-in at the company's gate and the truck unloading start time. We use this time interval the index to our results. So it has all these combinations and then we just compare those time intervals to find out the best policy.
David Correll:
Excellent. Thank you. And to Roger, what did you learn? What are the lessons from the research?
Roger Marino:
From what we learned from this project, we were able to determine that by keeping a constant unloading policy, the results were better than having the current approach, which was having a warehouse manager make these decisions and this is because their decisions were not consistent. And also that by knowing ahead of time, like if there's going to be a spike in demand, you're able to adapt each policy to the one that fits better, and once you're able to do this, your results are going to be better instead of having just an inconsistent but conservative approach from the warehouse managers.
David Correll:
Based on those takeaways. What is your advice to a warehouse manager?
Zeyu Wu:
Sure. I think warehouse managers should like knowing more, collecting more data about the truck arriving behaviors, then they can identify what's occurred in these situations or what about the next situation in the warehouses, then they can choose the best policy to unloading the trucks more efficiently.
David Correll:
Is there anything, when you were doing the project that surprised you?
Zeyu Wu:
For me, I think I learned it's quite interesting that the warehouse is a whole thing like it operates, it won't operate separately like say today only inbound, tomorrow only outbound, or other days only warehouse operation. So I think I learned when we do the simulation model, we'd have to concern the warehouse decision as a whole. We cannot just separate them and do only one part.
Roger Marino:
Yeah. So for me, one of the most surprising things that I learned is that the overall waiting time for trailers inside the warehouse, of which the average was like 21.5 hours. So in the US, I know there's a shortage of trailers and this not only happens in our sponsor company but throughout the industry. And I believe if the trucking industry is able to reduce this waiting period, it will become a lot more efficient than what it currently is and they might not necessarily need more drivers. So you just need to become more efficient and just shortening these waiting times.
David Correll:
What Zeyu and Roger's simulation suggests to us is that inbound scheduling should vary based on the demand that is experienced and expected on any given day. And at least in fast-moving retail, some demand variations are predictable, notably, the quarterly push of inventory as suppliers try to get their product move off their accounting books. When this is the case, dedicating dock doors to labor-intensive freight unloads works to reduce time spent waiting. However, in other cases, including business as usual and periodic storms, that same policy is the worst. We are committed to continuing to explore this fruitful area of research. Why try to get this right? Well, because the truck driver resource is scarce and dwindling and because in all systems, time is money. Maybe that's all you really need to know, but you probably already thought of that. Let me offer one more. Let's start with Mark. What would you want a shipper or receiver listening to this to know about the working conditions of the drivers carrying their loads?
Mark Cavanagh:
They all around need to change their attitude towards the drivers. We're not just hauling their freight. We're also providing for the country. We are essential to this country and they need to understand that and treat us with a lot more respect than what we're getting.
David Correll:
At a time when as a nation we are hopefully starting to come out of a pandemic that if you are listening, you unlike many survived, then perhaps we should now reflect on the many efforts that enabled our survival. In addition to the never repayable efforts of frontline healthcare professionals over the last two years, the rest of us, like you and me, the work from home podcast listeners, the plain and ordinary citizens of the homebody economy. We all made it through in relative comfort in part because of what truck drivers did for us, what they sacrificed to keep our supply chains running, the lengths that they traveled to make the homebody economy possible. It behooves us as researchers, I think, to now bring our skills and our focused attention to the problems that truck drivers face. Maybe we can't solve everybody's problems, probably not but efforts like this one are at the least I hope, a respectable acknowledgment of a very large debt. If you liked this, please stay in touch with me and the Driver Initiative to see what next year's crop of students and I come up with.
Arthur Grau:
All right, everyone. Thank you for listening. I hope you've enjoyed this edition of MIT Supply Chain Frontiers. My name is Arthur Grau communications officer for the center, and I invite you to visit us anytime at ctl.mit.edu or search for MIT Supply Chain Frontiers on your favorite listening platform. Until next time.