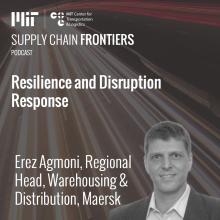
Resilience and disruption response with Erez Agmoni, Regional Head of Supply Chain Warehousing and Distribution - America at Maersk
Join MIT CTL's Alexis Bateman in conversation with Erez Agmoni about disruptions, supply chain design, and resilience tips for the supply chain and logistics professional. Interview recorded as part of mit.ctl.sc3x - Supply Chain Dynamics. Learn more about these free online courses here.
Transcript
[MUSIC PLAYING] Narrator: Welcome to MIT Supply Chain Frontiers, where we discover the future of global supply chain, education, research, and innovation. Brought to you by the MIT Center for Transportation and Logistics, every episode features Center researchers, and staff who welcome experts from the field for in-depth conversations about business, education, and beyond.
Today, CTL Research Scientist and Sustainable Supply Chains Director, Alexis Bateman, speaks with Erez Agmoni, head of Supply Chain Warehousing and Distribution America at Maersk. Take it away, Alexis.
[MUSIC PLAYING]
ALEXIS BATEMAN: Today we're really fortunate to have Dr. Agmoni with us. He is the regional head of Distribution and Warehousing for Maersk. He has a bachelor's, master's, and PhD from Assumption University in Thailand, and 20 years in logistics and supply chains.
EREZ AGMONI: Thank you, Alexis. As Alexis mentioned, I'm looking after the warehousing and distributions for Maersk for North America. I did a few different roles in the company. My previous role was supply chain design and engineering, so we were looking after supply chain of large customers and finding solutions for them to improve it. And that kind of gives some insight to the work I'm doing today, and bringing quite a better understanding of what is it that we should do for our customers.
ALEXIS BATEMAN: Erez, thank you so much for taking the time to join us today.
EREZ AGMONI: Thank you very much, Alexis. I really appreciate and honored to be here. And so what I'm about to share is a little bit an insight from the way Maersk is seeing things right now. And definitely, the Maersk perspective is coming from a global supply chain. But today, what we're basically doing is an end-to-end supply chain for customers. And that's allowing us to basically get and support the customer's request.
If we take 10 years ago, we had the volcanic ash cloud over Europe. In Iceland, there was an eruption of volcanic ash that basically disrupted totally all the flights into Europe. That caused a huge supply chain disruption. People that needed to move goods fast didn't have the ability to do it by air freight. And that kind of created some disruption for the Europe continent.
Just a year after, in Japan, Fukushima meltdown. In that region, in that area of Japan, there is certain memory that has been produced, and that's created some supply chain disruption, at least for the PCs and computers and high-tech industries. So similar to that, in Thailand, at the end of 2011 and the beginning of 2012, we had the floods in Thailand that-- and Thailand is the capital of the world in terms of hard disks. That created a huge disruption into the tech industries.
A few years after that, 2014-15, the West Coast labor strikes that shut down ports. In 2017, Maersk was one of the impacted by the NotPetya virus. All our system went down within a day, and no more IT system to support operation. And that was-- Maersk is the largest carrier in the world, with about 20%, 25% of the ocean containerized logistic. That's created a huge disruption in the market. It was not only us, of course. It was many other companies, but only that and the ports that related to that, it already was a huge disruption.
Of course, COVID-19 that started at the end of '19, and we are in the middle of it right now, that's creating and bringing the awareness of disruption once again. With that in mind, you can see that, of course, it's pandemics, but it can be a human-made problem. It can be natural disasters. It can be laborers' availability and strikes. It can be IT failure and IT-related, which is also kind of man-made, definitely bringing us to we need to get prepared. We need to be ready. If you're not ready, there is a huge potential for companies collapsing. And I'm sure that some of the companies will not make it and will not survive this current disruption.
Those kind of unpredictable market demands and volatility create different needs for supply chains. You can get requests from customers to get cargo much earlier in their supply chain. Or in their DC, you can get requests that the warehouse is full. You need to actually change things. You can get requests, please bypass these DCs and go directly to final customers or to the store. There is a lot of different requests that supply chain needs to be started to look into and become much more flexible than it used to be. You cannot just have a supply chain that is built on one set of rules, and you don't have a backup to that. Flexibility, speeding up, slowing down, it's definitely a key to sustain volatility in supply chain.
One of the things that can support such design of network is a promise of an end-to-end lead time guaranteed. A normal transit time from Asia to the US, for example, from the moment it's ready at the factory until it's arrived to the DC, it's around the 40, 45 days, plus/minus 13 to 15 days. This is a huge variation across the supply chain. It's very difficult to plan and decide things based on such a huge variation. Reduction of that lead time variation is definitely a key to the future of supply chain improvement and resiliency.
Visibility all the way of your supply chain, 100% visibility is crucial to have it. And you need provider or support from providers that have end-to-end capabilities to actually execute the supply chain as such. For example, you need to come within certain amount of days form a region in Asia to a Memphis DC. The easiest way to do it is, of course, coming to the West Coast and enter over there. And of course, truck from there to Memphis, you arrive to the destination.
But is it the right way to do that? Probably for certain times, but not always. You definitely need the flexibility to say, hey, now I don't want to go from the West Coast. I actually want to delay it. I'll come from the East Coast. Or maybe I would first bring it into a DC or a warehouse that can actually store it for a while and act on it only when I need it. Or some places-- a deconsolidation place that can actually give me the ability to go and distribute it to different destinations. So that can actually be across those kind of capabilities.
I'm sure that you feel that, oh, wow, with all this flexibility, it definitely must cost me more to run such a supply chain. But my answer to that is not always. This is just an example of an end-to-end reduction of liability that we worked with one of our customers. Originally, it was about 40 days with a plus/minus 13, so anywhere from 27 to 53 days that they can arrive to the destination all the way from origin.
We built a solution that is 29 days, plus/minus 3, so yes, in the origin solution, you can come at 27 days. You have a good chance to come very fast. But at the end of the day, there is a lot of uncertainty when this will arrive, when cargo will be there. And that's creating a much more inventory acquisition, and we're basically starting to build more inventories in a warehouse which costing us definitely a lot more money. So we're using that inventory. The safety stocks in our warehouses basically help to actually reduce the final amount of money that we're spending on our supply chain.
Another quick example on that is an example of a normal regular solution where cargo arrives at the port of-- this case is in LA. It has been-- basically goes to the final port, the inland port, so there is another move of the 40-foot containers goes to the surrounding of Memphis. And then from there, you have another provider come and take this 40 and bring it to the final. Here is actually Fort Worth-Dallas. There is multiple handovers, and your 40-foot container is keep moving around. And actually, this is the one that they're moving to the final destination.
Because of the multi-vendors and multi-handoffs, the transit time from arrival to the port, all the way to destination is something between 6 to 10 days, something that you have a variation. The cost of that is actually more expensive. An alternative to that is basically you taking it into a warehouse located very close to the port. You convert the 40s into 53 trailers. You can save on environmental impact. You can save on the movement of 53s that actually move to your destination.
And you can create much better accuracy of the transit time. And we can see in this example that we have eight to nine days. So yes, it is still higher than the six days that we have in the original example. But it's definitely much more accurate, and you can plan much better around this. And of course, at the end of the day, it also creates some cost reduction to the customer. Here in this case, it's $300 savings.
Yes, it sounds more expensive to have flexibility and solutions, but there are ways to actually go around it and create some kind of measurement to actually help you to save. Having all those type of operations definitely help, but it's not all. You need to build solution in advance. You need to build ways to be flexible. But you also need two kinds of things-- what alternative do I have for certain things that I'm depending on?
And as I mentioned before, one of the things that can create some disruptions is actually the human being. We have shortage of human being work willing to working in certain environments. And I'm not thinking that people will disappear from warehouse anytime soon. But definitely, we need to have alternatives, and we need to have certain potential ideas.
Just certain things that we are working on, this is an autonomous vehicle that we are testing basically, in the yard. And the idea of that is to create another set of pool, for example, in the middle of the night, when people do not prefer to work in those shifts, we can actually rearrange all the containers in the yard and bring them into the right position that we can actually work early in the morning when people arrive.
Another solution that we're exploring right now is container unloading. And there are different type of machines doing that today, going inside the container and starting to unload cartons and bringing them to a conveyor that wait behind that and start to sort. I'm calling this machine the Cookie Monster. It sounds like it's to going inside and eating the boxes with suctions and with other kind of equipment that bringing it in a much faster speed than we could do manual.
Beside the automation, of course, any company that would like to be ready for such a disruption or such a volatile time need to build a business continuity process. The number one is to ensure that safety of people, and then you have safety of infrastructure. That's the second thing. If your infrastructure is still available, accessible, that definitely help you to be able to work on solution and create solutions.
Of course, there could be times that infrastructure goes under the water, for example, literally in Thailand, the floods, or other different things that you just can't access this infrastructure. Then you need to have some continuity planning. Where are you going to move people? Will they work from home? Will they work from a different location? So the crisis management is the next thing that needs to be executed.
A structured training crisis management team needs to be in place and needs to be the one that's handling everything. We call it the War Room, basically, people that are capable to give the right communications, ensuring that people are getting one source of information and correct source of information. It's very crucial to success in managing any crisis.
And then at the end of-- after these initial plans, the business continuity planning needs to take over, creating a business risk assessment and ensuring that all the offices, we have documentation of what you do, how you do things, what is happening with the operation, who is doing what. For example, what happens if you have somebody infected with the coronavirus in your facility? What is it that you're doing? How will you return to normal operation, and making sure that the operation is really capable to do that.
Of course, the process needs to be preplanned with the business continuity planning. You need to document and ensure that you have the right infrastructure, people knows how to do things, even they are not in the office. IT needs to be supported. The first few days of this coronavirus, we saw that our IT bandwidth started to get heated by all these conference calls and video calls, took about two days to execute the plans, and we're back to normal operation. But people could actually do all those video conferences and video calls over the internet without disruption. So that is definitely one of the key things in order for us to success in mitigating those kind of situations.
ALEXIS BATEMAN: Great. Thank you so much, Erez. That was really insightful, really interesting, and brought some good perspectives. My question is, how do we deal with this when it's such an extended situation, where it's going to-- it's not a few days long. It's not a few weeks long. It's going to be months long to a year long? How do you see Maersk responding in that way, and in general, any suggestions you have for those online.
EREZ AGMONI: Definitely, the number one thing, as I mentioned, is definitely ensuring the safety of the people, both our own employees, and the people around, and everybody in the community. So that's the number one priority that we have to take care.
The second thing is communication. We have to build some communication methods and skills that ensure that the visibility keeps going and people understand what is it that's happening. The whole chain needs to be communicated constantly, even daily or multiple times a day. Definitely, if it's becoming an extended impact and situation, I do suggest-- and I think that we are also taking the same approach-- is delay unnecessary projects. You will need the cash very soon. Things will change. And in order to free cash, any unnecessary project, delay it or stop it for now.
One of the things that we see with our customers, the feedback that we get from them is that they're really happy that they're working with a logistic provider that can give them the flexibility and the solution on the end-to-end, so alternative routing, alternative solution, different ways to do things and make sure.
And I think one of the important things to remember is don't panic. Everybody learn about the bullwhip effect. When it's reached to a point that we're starting to react with no control, we're creating huge supply chain effects. And that's definitely something that needs to be thought and planned and see, do I do it because I'm panicked? Or do I do it because this is the right thing to do?
ALEXIS BATEMAN: Supply chains were largely invisible to the lay audience, to the public, to many people. And now they're in the limelight. We're seeing the critical role of supply chains. Can you talk a little bit about what you think the emerging role of the supply chain professional will be?
EREZ AGMONI: So I do advise people to keep search and explore for alternative out-of-the-box thinking and ensure that the business continuity plan is exist. It's crucial to have it, and make sure that you and your provider have those kind of planning around.
ALEXIS BATEMAN: Are there things-- and you've alluded to these, but maybe pinpointing them in some future-oriented practices-- that companies can think about now to internalize as we enter a period of recovery?
EREZ AGMONI: So I think it's a lot for us to do, to build for the future, to be ready. One of the things will be to build a cross-functional team, senior management and experts in different fields, just to be sure that we are addressing all the supply chain risks, and we're preparing for them. We call it War Room in the bigger scale. And when we talk about different locations, we call it cockpit. So definitely, that's an important thing to do and to plan for.
Decision that you make, definitely make those decisions to protect the bottom line. Know the procurement cost. I will challenge you guys to think about the bigger picture, the bottom line, and protect that one. Definitely, this is important.
Another point is definitely to develop supply chain visibility. Without visibility, you cannot take action. You are basically-- goes in the dark. And we see that in certain companies that do not have the visibility. They have no clue where the cargo is, where the PO is, when it will hit this location or that location. So in order to actually have actions, you need to have the visibility. So that's definitely something to be prepared for.
Use more integrated supply chain providers. As I mentioned before, it helps with the flexibility, the visibility, and the reduced time to market. Of course, if you can, consider multi-country sourcing or different locations to be sourced from, not always easy, but definitely something important to think of. Definitely request your supply chain providers to share their plans for disruption times. So if they have any plans, that definitely need to be shared so you can actually work together to come up with solutions for that.
ALEXIS BATEMAN: This is great. Thank you. One question from Amanda is, is the Cookie Monster also available for pallets?
EREZ AGMONI: So yeah, I saw solutions that are available for pallets. It's not exactly the way the Cookie Monster work, but it's going to be, I don't know, a mini Cookie Monster. There are solutions to unload the pallets from containers.
ALEXIS BATEMAN: Is the Cookie Monster doing damage to the packages, cartons, that are moving through?
EREZ AGMONI: So the testing that we are looking after, there is basically so far was no damage, or less than 1% of damage in the one that we tested. We are testing a different one right now that is basically zero damage. It's moving as fast as the Cookie Monster but in a different way. And that's different zero damage for now.
ALEXIS BATEMAN: Great, thanks. So Crystal asks, what do you see about the trend for-- and we're going to try not to get too political here but-- deglobalization? Is there a trend for dual supply chains to cope with these global trends and your perspectives on that?
EREZ AGMONI: Definitely, it will impact-- the supply chain prices will change. People will have to rethink where they're sourcing their goods from. But that brings us back to the ideal of let's create more than one locations that we're sourcing, because even if we want it or not, we cannot just eliminate China or eliminate Mexico or eliminate somewhere else around the supply chain.
There is going to be always a need, both from supply and from demand, to keep working with the whole work. I know that there is a lot of different voices nowadays that we need to definitely look at our own people first. But if we want to keep the way of living that we live today, and all the accessibility that we have to products, we definitely will have to keep the ability to work globally rather than just locally.
ALEXIS BATEMAN: So then we have a big question from Sumia. How does Maersk incentivize supply chain partners to share data?
EREZ AGMONI: I think the best way to incentivize people that can share data is to give them data back. So that's the best way to do that. We have to also remember that a lot of the data that we have is actually generated from within the company, because we own both supply chain management. So we have all the information from our customers on the PO level. We're helping with the vendor management. We have that information.
We have the ports with the ATM terminal ports. We have the vessels themselves, so many different types of information is already coming within the company itself. Of course, it's limited for our own kind of capabilities. So when we need airfreight type of information, or other carrier information, trucks information, definitely the number one is give and take. The second one is, of course, you pay per use when needed.
ALEXIS BATEMAN: All right, thanks. So now this one's going to really press our brains here, which is we have this ongoing crisis with COVID-19, and now in Southeast US, we'll soon have a hurricane on top of the COVID situation. Does crisis response or planning take into account multiple emergency events at one time? And what are your thoughts on that?
EREZ AGMONI: Definitely, multiple things needs to maneuver, then take care at the same time. I think it will impact the way we work. It's going to create-- look at things in a different way. The way we are handling that, as I mentioned before, is having a War Room, plus cockpits in the different sections within the company to ensure the flow of information and flow in communications is coming and going from the different angles of the business that is moving around.
ALEXIS BATEMAN: Right. So Musas asks, are you seeing a difference in how companies are moving their goods? Are there certain trends you're seeing there?
EREZ AGMONI: Oh, definitely. Definitely, there is a huge change, 180-degree change of the way people used to do things until a month ago and how they're moving today. The number one thing that we see is a huge request for air freight and charter, air charters operations. And this is everything that needs to be done fast for all the medical support and the sanitarium equipment, et cetera, et cetera is today moving by air freight. There's no ocean involving that. There is, but the number one thing is going by air freight, so huge constraints.
And remember that most of the capacity in the air freight world is in passenger aircraft. I would estimate it to be 60%, 70% of the world's capacity is actually in the belly of passenger aircraft. When those aircraft are not moving, we are moving to charters. And there is a certain amount of charters or freighters available in the market. So we see airlines that are taking the seats out of the passenger or other airlines, then putting cargoes on top of the seat and putting nets. So that's number one thing that's happening.
When we're talking about the oceans, a lot of the distribution centers are full and closed. And they cannot take more cargo anymore because all the stores are closed. And there is no release from the DC, so people are looking for store containers for us. Can you reroute it? We have different locations, so it will arrive later than before. So cargo that used to go into the West Coast now have been requested, please route it in to the East Coast. Let's gain another 10 to 2 weeks' time on the water so we don't need to find solution for that. And by then, hopefully, things will change.
People are asking to-- they want to reduce the detention, [INAUDIBLE] on the containers. So they're asking for solution to get off cargo and put it in temporary storage in warehouses, get different requests of, can you now break the cargo, take only the emergency goods of the things that needs to be used for emergency, bring them to the final destination, and the rest you hold for now? So there is multiple different requests nowadays to change supply chains of the customers.
ALEXIS BATEMAN: Right, no, super interesting, thinking about all the different changes going on right now. So David asks, is Maersk making agreements with third parties for increasing capacity, or is that managed internally? Any additional advice related to flexibility?
EREZ AGMONI: The simple answer in terms of, do we do capacity management with others? The answer is yes. There is alliances in the world today. And definitely, each carrier has backups, including Maersk, with other carriers and increasing capacity. But the main flexibility is not coming just because of you get more capacity. A lot of the time, actually, the carriers would like to reduce capacity because it's impacting-- you cannot operate a capacity if it's not bringing a certain amount of income, because otherwise, you're actually losing money for every voyage.
So there is a lot of times that you actually reduce capacity just to maintain certain rates. But the real potential thing in order to create flexibility is to be able to have your own capacity and control of every element in the supply chain. So if for example, the ocean port to port is being slowed down because of whatever reason-- and always, something can happen. You cannot create a bulletproof point to point supply chain. You can create a much better resilience end-to-end supply chain by being able to actually control everything in the supply chain and mitigate those problems along the way.
So if you have all the end-to-end capabilities and the ocean portion is actually being delayed right now, or alternatively, arrive earlier, you can actually slow down or speed up when you move things through the warehouse or through the trucking or through-- so that's basically the way we're creating flexibility. And on top of that, you have to have the visibility. As I repeatedly again, visibility is the key for everything.
ALEXIS BATEMAN: Do you have a prioritization or a classification that Maersk prioritizes humanitarian cargo, and how do you deal with that?
EREZ AGMONI: Yes, definitely. We have a government and aid section within the company that supports FEMA and all the other kind of global organizations that definitely gets number one priority for these type of equipment and goods that needs to support the life of people. We are prioritizing.
ALEXIS BATEMAN: Jose now asks, could you say something about the current shipping container shortage?
EREZ AGMONI: Definitely. A lot of the cargo, as I mentioned before, has been stored in containers nowadays. People are asking to find solutions for the yard and impacting the ability to move containers into their location. Certain companies that needs those containers for exports, we see them willing to pay money to move empty containers from the ports into the inland portions of the country. Certainly, it's something that you don't see in normal days. Normal days, they are taking advantage of the empty containers being in those places. But nowadays, when you have a shortage, people get creative and find a solution together.
But the more cargo will be stuck inside the containers, the more we'll see shortage with that. And we'll have to find alternative solutions. One of the ways could be to move things in the '53 trailers, bring them into the ports, if you need to export, and basically convert it back to 40s in the port area. That could be an alternative solution that we're working with some of our customers nowadays.
ALEXIS BATEMAN: Thanks for that. So another question, Sorren is asking about oil prices right now and the fluctuation. How is that impacting Maersk's strategy in any way?
EREZ AGMONI: So I'm not an oil expert, but I know that the way we are dealing with oil is based on the market. We're not bunkering any oil or fuel in advance, because that's kind of becoming more of a gambling exercise to understand. So we've taken and pushed back this up and down with the customers, and we work with them to ensure this is a sustainable tool.
ALEXIS BATEMAN: Carlos asked, do you think this global situation will create new business models for the supply chain?
EREZ AGMONI: I am sure it will. I'm sure it will. As we spoke before, people are looking for different ways to move the cargo. I think, at least the way we see it internally, one of the key things to enable companies is the end-to-end supply chain guarantee of transit time or reduction of variation.
ALEXIS BATEMAN: So [INAUDIBLE] asks, in Maersk, is there a team or any individuals fully allocated to emergency response crisis management?
EREZ AGMONI: Oh, yes, definitely. There is a team. They're dedicated to that. We have the protocol of-- these people are not sitting idle the whole year round. They are coming from the different businesses, and they're part of a disaster recovery team. And the moment that something goes on, basically, we initiate this team and bringing them back to the War Room, and ensure that there is an execution of the plan that we set in place. So those teams are fully aware of what they're supposed to do. They're part of the regular discussions in building up the recovery plan during the year, so yes.
ALEXIS BATEMAN: Great, thanks. So we're coming to the end of this awesome session. I just want to thank you so much, Erez, for taking your time. I know you are managing a million things right now, so I really thank you for taking the time. Final, final question, any words of wisdom as we sign off?
EREZ AGMONI: I can only offer wisdom when in supply chain. [CHUCKLES] Definitely, see the bright side of things. Supply chain is being disrupted, but it shows that it's necessary to plan and necessary to building. So in the last 10 years, we repeatedly have different disruptions, maybe not in this magnitude that the whole world is shut down, but there are constantly things that are disrupting our supply chain. And when it happens, people, yeah, we need to do that. We need to do that. And then the moment it's over, yeah, let's go back to normal. We forget about this.
So definitely, I encourage you to work on that. Make sure that you have this protocol in place, and you actually refresh them within time and checking that they're still valid and workable. People that might be impacted in the short term in terms of work, I believe that you're definitely going to find yourself in a good situation after it's all over, when more and more companies will want to have those expertise and capabilities in place. So definitely, remember that.
Keep doing the good stuff that you are doing, because I think people that are in the supply chain are the number one crucial to make sure things are moving and flowing, so definitely, a good job for everyone that's involved in supply chain.
ALEXIS BATEMAN: Thank you so much, Erez. Those were great words of wisdom to sign off by. Thank you, and everyone stay safe and healthy.
ARTHUR GRAU: Thank you, guys. All right, everyone, thank you for listening. I hope you enjoyed this edition of MIT Supply Chain Frontiers. My name is Arthur Grau, communications officer for the center. And I invite you to visit us anytime at ctl.mit.edu, or search for MIT Supply Chain Frontiers on your favorite listening platform. Until next time.
[MUSIC PLAYING]