- Demand Planning
- Forecasting
Engineering projects carried out in harsh environments require a reliable supply of spare parts. However, providing such a service is challenging when the demand for parts is intermittent and procurement practices lack cohesion.
A thesis project completed by Sachin Shedge, a graduate of the MIT-Malaysia Master of Science in Supply Chain Management program, explored the supply challenges of engineer-to-order (ETO) supply chains. These issues have not been studied extensively in the extant literature. In particular, Shedge considered what demand forecasting method is best suited to an ETO environment, and how such a method can integrate the supply chain’s customer- and supplier-facing functions. Dr Javad Feizabadi, Director of the PhD Program and Winter Academy at the Malaysia Institute for Supply Chain Innovation (MISI), supervised the work, and the thesis sponsor is a leading oil and gas field services company.
The research focused on a unit of the company that sells seismic analysis services to customers. These projects employ several types of equipment that require a wide variety of spare parts. Demand for the items can be erratic and difficult to forecast. Moreover, the projects usually take place in remote locations, and although the company has a centralized procurement function, it is usual for chief mechanics in the field to be responsible for equipment maintenance.
These managers use their intuition and judgment to order spare parts from the sourcing function, which resides in a Shared Service Center (SSC) located far away from field operations. The SSC is structured in such a way that it can take advantage of economies of scale, but it lacks specialist knowledge of the parts needed by field operations. This shortfall increases the need for effective, cross-functional integration. The company’s centralized procurement function is a long distance from project operations.
The thesis research included both qualitative and quantitative data.
Qualitative data. Three people from field operations and five individuals in the SSC were interviewed about the process of integrating customer and supplier facing functions. All the interviews were semi-structured and lasted for 45-60 minutes each. A set of open-ended and semi-structured questions were developed following background questions from the interviewees. Field notes and verified summary versions of interviews were used to identify patterns in the answers of all participants.
Quantitative data. Archival data for three representative projects were gathered from ServeOil, that delineated spend histories for all the resources that were acquired over the life cycle of the projects. One project was dropped due to incomplete data. The spare part demand data were categorized, and it was found that most of spare parts fall in intermittent and lumpy demand categories.
A key finding of the primary data analysis is that information quality, procedural quality, alignment quality and the degree of constructive engagement are important in the context of improving integration between customer and supplier facing functions. This is significant finding in that it pertains to a project-based operation and the organizational structure of a shared service center.
Another key finding is that the planning process plays a pivotal role in integrating customer and supplier-facing functions in an ETO supply chain and SSC organizational structure.
The results of this study can help project-based operations to improve the efficiency of the pare-part supply chain. Many firms changed the organizational structure to centralize their procurement activities and exploit economy of scale. However, they face a lack of integration in their supply chain, particularly in the case of spare parts which have very unpredictable demand. Also, projects tend to be sited in different geographical locations, and there is a disconnection between procurement and operations.
Having a planning process as described in the research (see Figure 1) would help firms to yield better performance in terms of demand forecast accuracy and effective fulfillment of field operation’s demand. Such a process would also help firms to exploit the benefits of supply chain alignment, without changing functional incentives or organizational structure.
As depicted in Figure 1, information quality describes the effective and real time information sharing among customer- and supplier-facing functions. Procedural quality refers to the use of appropriate analytical tools to process the data. Alignment quality explains how well the interests of customer- and supplier-facing functions are aligned, and constructive engagement focuses on the active participation of those functions in the planning process. By applying these concepts in the case study, it was found that these features are relevant for achieving integration in an ETO supply chain.
This article was written by Sachin Shedge and Dr Javad Feizabadi. For more information on this research project and the MIT-Malaysia Master of Science in Supply Chain Management program, please contact Dr Javad Feizabadi at jfeizabadi@misi.edu.my.
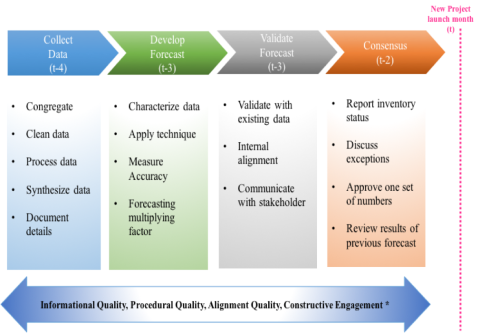