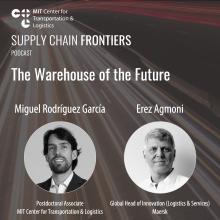
Warehouses are undergoing a fundamental transformation—in response to the explosion of growth in the e-commerce space and worldwide large-scale supply chain disruptions, warehouses have gone from places simply for goods to sit to highly interconnected, automated hubs of activity. Warehouses of the future leverage new technologies in automation and digitalization to enhance precision, flexibility, and efficiency to adapt quickly to changing market and supply chain trends and needs.
In this episode, we're joined by Miguel Rodríguez García, a Postdoctoral Associate at the MIT Center for Transportation & Logistics, and Erez Agmoni, Global Head of Innovation (Logistics & Services) at international shipping giant Maersk. Miguel and Erez take us through the changes and technologies that are transforming warehouses and the ways in which companies are seeking to make these transformations sustainable.
The warehouse of the future signifies a forward-thinking model that aligns operational efficiency with a sustainable approach to warehousing, which is pivotal to the evolution of contemporary supply chains.
For the full white paper, "The Warehouse of the Future," click here.
Transcript
- Welcome to MIT Supply Chain Frontiers presented by the MIT Center for Transportation and Logistics. I'm your host, Benjy Kantor. Each episode of Supply Chain Frontiers features center researchers and staff or experts from industry for in-depth conversations about supply chain management, logistics, education, and beyond. Today we're talking about the warehouse of the future with Erez Agmoni, global head of innovation for logistics and services at Maersk, and Miguel Rodriguez Garcia, postdoctoral associate here at the MIT Center for Transportation and Logistics. First, MIT CTL offers a variety of educational programs for graduate students, seasoned industry professionals, and anyone at any level looking to learn about the supply chain and logistics domains. To find out more about all of CTL's educational offerings, visit ctl.mi.edu/education. Today we're pleased to welcome Erez Agmoni, global head of innovation, L and S, at Maersk, and Miguel Rodriguez Garcia, a postdoctoral associate at the MIT Center for Transportation and Logistics. Dr. Erez Agmoni has a wealth of experience in the supply chain field, more than 25 years, supply chain management, freight forwarding logistics, engineering and digital innovation. In his current role, Erez heads the Maersk Innovation Center, an in-house team of experts in data science, engineering, entrepreneurship and thought leadership, brought together to spearhead new initiatives and steer innovation in the right direction. We're also joined by Miguel Rodriguez Garcia, postdoctoral associate here at MIT CTL. Miguel works in the omnichannel supply chain lab at CTL, where he has the expertise in procurement, warehousing, manufacturing and transportation, with a particular focus on e-commerce and omnichannel logistics, currently working on research with the omnichannel supply chain lab about the future of supply chains and warehousing in the face of expanding e-commerce and technology developments. Erez and Miguel have just completed a white paper exploring the warehouse of the future and how that can help companies strengthen their supply chains. Welcome to the program, Erez and Miguel. Thank you for joining us.
- Thank you. Thank you for having us.
- Absolutely. The warehouse of the future is a pretty broad term. Let's start with the brass tacks. What specifically do you mean by warehouse of the future?
- When we refer to the warehouse of the future, we think of a highly-automated facility, an interconnect system within the supply chain that leverages digitalization and automation as two key aspects for this transformation. And this is important 'cause automation and digitalization together can bring the required speed, flexibility, and efficiency that the current market trends are actually demanding at this point. So the third key aspect of the warehouse of the future is the sustainability aspect. There have been many research studies in the last few years suggesting that they're real important contributors to global climate change and greenhouse emissions. So up to 3% of all the greenhouse emissions in the world can be related to warehousing, or up to 25% of all the greenhouse emissions from the logistics sector. So really important contributors to this.
- And Erez, this is your opportunity to argue right off the bat with Miguel, but-
- I'm not gonna argue. Definitely he brought up an amazing points here that makes a lot of sense. And we select those three points together, of automation, digital, sustainability. But I think it's important to mention that warehouses play important roles in the end-to-end supply chain. They're in between so many moving parts and non-efficient work in the warehouse is bringing our supply chain down into the level of very low productivity. Consistency is not there, you know? You have one warehouse that's doing something in one way and the same goods in the same manners in a different warehouse, suddenly you have different people that acting slightly different, and then the results is so different. So in order to improve supply chain, at the end of the day, you need those elements, each of the elements. And the warehouse is a very crucial element there to be consistent, to be bringing the productivity up to the maximum that you can squeeze from that four walls because at the end of the day, you don't want to keep opening more and more locations every time you're slightly growing. You wanna be able to have that flexibility of up and down because that's seasonality there. That is a very important element to talk about how warehouses should look in the next few years. I'm not talking about 20 years ahead or 30 years ahead. We're talking about something that is already here and needs to be completed very, very soon.
- So what's the practical application within the Innovation Center at Maersk for this concept of warehouse of the future? Like, you know, Maersk is a big thing, it's a big operation. You know that.
- Absolutely.
- And so I'm wondering, like, at a very practical level or even, like, a simplified level what that means for you as opposed to other companies or organizations.
- So just two sentence about why Maersk. A lot of people think Maersk is a shipping line, which is definitely true, but Maersk is also a global integrator of supply chains, right? At the end of the day, it's a end-to-end, and trying to help customers to improve their supply chains all the way from the beginning, all the way to the end. Now, what are we doing in the Innovation Center? We have three main pillars that we are working on. The first one is automation and autonomous. So a few examples is robotics, robots that doing things that people don't want to do. There is so many jobs in the warehouse that you hurt your back, you hurt your, you end up at the end of the day, and it's like, "I don't want to come back to this job." Right? You have so many other options nowadays that you can actually do and control your own schedule, your own life, and you actually shift. Those people shift to those type of roles. They don't want to come back. So that is one element that we're working on. The other one is the digital. So the digital elements or the digital innovation, we are working on digital twin for our warehouses. We're working about different computer vision that's supporting by machine learning and AI to help improving productivity, improving the way we're working and creating a much better way for how we're working inside the warehouse. And the last pillar that we have in our Innovation Center is actually product innovation, when we take really the end-to-end supply chain, and now we're trying to bring it all together to support an improvement for the customers to how you can actually bring goods in a much more concise transit time. How do you help them to reduce safety store? How do you reduce the amount of work that is actually going to warehouses? It feel like you're shooting your own legs, but I feel that this is, and I know that the company behind us is you're actually trying to create value for the customers by improving and reducing the movements. So you, in one hand, you're gonna get less business, but it's gonna be much more quality business that you get.
- So how do you contrast or what is the contrast between the concept of the warehouse of the future and how warehouses are currently designed and operated right now?
- So I think looking back, I don't know, 20 years, I started working on this only 10 years ago, but the transformation, I think, has been huge. Most of the warehouses in the past looked pretty much the same. You had pallets, you had palletizers, you had forklifts, pallet trucks. And then e-commerce came. That was, I think, the first key driver of the transformation 'cause you went, or many companies went from just moving big unit loads to actually started moving cases and hitches. So that actually brought a huge change to the warehouse space. That, in one sense, meant that picking became a key process within the warehouse. We include things like distribution centers, fulfillment centers, which I think is something important for people to have in mind that our idea of the warehouse takes many facilities into that. So e-commerce, big transformation because of the changing unit loads and also the customer requirements. The customer expectations with e-commerce, and because of Amazon mainly, increased a lot in the last 10 to 15 years. So that meant that companies needed more speed, more accuracy and more precision and also more efficiency 'cause Amazon was getting bigger, doing everything cheaper and cheaper. So that meant that warehouses had to change and transform. So I would say that that was one of the big, big changes that we saw in the last 10 or 15 years from the type of warehouses that we had in the past that was mainly storage facilities to what we have nowadays, which are facilities that add value to the supply chain in different ways, like more speed, more flexibility, more efficiency.
- Are you finding that things from your research that apply to these, you know, you've mentioned Amazon and Maersk, these larger companies, or that are just touching so many things that apply to smaller companies that are much more specific or individualized I guess?
- Definitely. I think there's so many things that those small companies, in order to survive against those monsters, they need to be much more efficient than everybody else. They need to be actually nimble, reduce their cost, be able to know exactly what they have, where they have it, how to ship it. All those elements needs to be even more. So we see a lot of small companies going in that direction. But I do wanna add some small, let's say, painting the picture of how warehouses used to look compared to what they're looking now. So one of my previous roles, I was heading our warehousing and distribution product in North America. So when I just entered the role, I ask, "Can I see a presentation of what we are going to our customers with?" And it was a few years back, and at that time, most of our warehouses were, at least North America, used to be a cross-dock type of warehouse deconsolidation, where you bring goods by containers, you split them into many DCs, fill up trucks, trailers, and ship it to those DCs, right? Today we have all the different type of warehouses here. But what I saw there was shocking because we were showing people pushing carts and another picture of a person with a folder in their hands and, basically, a pencil just, you know, to look I'm writing something out there. And I was like, "Doesn't make sense," you know? Even I knew that there is no much technology in deconsolidation warehouses at that time. I said, "This is not what we should be proud of," you know? "It's labor intense. People don't like this type of pushing and moving stuff and unloading things." But people push me back, "But we are experts in this. This is what we know how to do best." But I said, "How long more can you do that?" And luckily we started to change before COVID because otherwise, during COVID time, you won't be able to sustain. So today's warehouses, you see a lot of automations and a lot of robotics and a lot of digital aid devices. It's not there yet. We are not in the final game yet, right? Definitely we are starting to get ourself towards the right goal and be able to see everything, control everything, knows what's going on. And of course also, let's not forget the sustainability, where in the past you have warehouses that lights all day, all night, using a lot of old style of lights because just it's expensive to change it. People didn't even want to think about, yeah but you can return that change investment in, I don't know, probably a year, right, and change it to halogen, change it to a LED, change it to certain controls by movement area so you don't turn lights everywhere all the time. All those type of things actually you can start seeing them in the warehouse today, and in many, many places, you can start see how we're getting there. I think what we're missing, the last thing, is still the construction of the warehouses. We are getting there. There's very few companies that construct with materials that make sense for the future, but we are not there yet. And of course we have so many old warehouses, what you gonna do with them? So will take probably, that the element that will take the longest.
- It's fascinating to me when you talk about automation because I think to the lay person, which I consider myself with regard to logistics and supply chain stuff, as an end consumer, I go into CVS, I go into Walmart or the grocery store, and there's my lucky charms, and I'm like, "Oh, it got here. The automation worked, no problem. The robotic arm picked it up, it moved it over to this part." But also, at the same time, there's this flip side of I wonder if it's just a marketing perspective. I see, like, Amazon commercial, and you see just people running up and down aisles to grab things and package them together. So it's, like, an interesting, for the end consumer, I think there's, like, this, it's just a taking for granted confusion, "Well, it got here, so it worked," but there are actual people who are operating some of these things.
- I don't think that you're taking the people out of the equation anytime soon. All those robotic arm that picking this or picking there, they're far away from the productivity of people, especially in the picking. They're not there yet. And especially when you don't have the same product all the time. If you can repeat, if it's the same product all the time, that's easy, easy to define something. But when a robot needs to start changing, and now it's this and now it's that and now it's this, now it's starting to slow down. And yeah, there's some good stuff out there, but we're not there yet, I think, as society in general. But there's so many other things that human and people needs to interact in the warehouse. People will not disappear from warehouses anytime soon. Those dark warehouses that are being discussed, they could happen in certain type of warehouses when you don't have so many movements. But definitely we're gonna see, I think, in the next 10 years, a lot of work and integration of people and supporting the people to work much more efficiently because that is the main problem. You know, in one of the warehouses that we installed collaborative robots, so people used to walk 20 to 25,000 steps a day. I remember one of the ladies that I met there, and I ask her, "Well, how many steps you're doing?" It's like she show me her watch, and I'm like, "Wow, this is a lot." Then you introduce collaborative robots. So now they can stay in the aisle, and the robots go around and, you know, come to them instead of the other way around. Suddenly you drop it down. So their life is improved dramatically. Productivity went by double. You know, everything is going into a happy path like that.
- Yeah, you're not walking half a marathon every day.
- Exactly. And if you using actually goods-to-person robotics, now it's so much even better because productivity further goes up, and then people can sit in one location. They don't even have to stand and walk all day. So they can do up and down, sit and whatever they're comfortable with. But you reduce those type of elements quite substantially.
- So I think we agree on the fact that the most flexible automation you can have is still people. At the end of the day, this change and this transition is going step by step 'cause you need the flexibility of having people doing different things. And the automation is, Erez was mentioning, for example, this robotic arm like picking arms, they are not like us yet. I mean, we adapt to everything. But the transition is coming from that collaboration. And I think, for example, collaborative robots, which are these robots that work alongside humans to facilitate picking, that they're being implemented in many different warehouses, mainly for e-commerce, but also for other types of jobs. And we see that that transformation is coming in bite-sized chunks. It's not a, okay, I just go from nothing to a fully automated warehouse, but instead I'm adopting different technologies, automation, digital tools to actually increase productivity step by step.
- Erez, what are the steps one takes to end up as the Maersk global head of innovation?
- Good question. I think it's a way of life, way of living, right? I like to challenge things. I like to challenge status quo. For every role I did in my life, I always, like, "Why are we doing this way? Why are we doing it like that? Can I do it in a better way?" Basically, in multiple roles actually at Maersk, my previous role, for example, as a head of warehousing distribution, I was like, "What is this old manual work? Let's change that." So we started to run a proof of concept. So here is a small thing that we checked and here is another bigger things that we checked and change that. And we saw that it's actually requires a focus. There was no role like this before that I was just trying to apply. We created that Innovation Center from zero based on, you know what, we need to focus on those changes because nobody can do that while they do their day-to-day job. It's very difficult to both run the business but also change the business at the same time.
- I want to add this one thought here. Okay, what about all these smaller companies that are not Maersk or that don't have access to a lot of capital to investing in this transformation? So we see in the omnichannel supply chain lab, we have been researching about the new business model of robotics as a service, which has been increasing quite a lot in the last few years, and it's, basically, a subscription-based model. So if you're a company that is operating in, for example, the e-commerce world, and you need to increase efficiency in your operations, and you're looking at an investment for a new automatic storage and retrieval system, you might be looking at investment that is millions of dollars. As a small company, you might not have access to it. So we see a lot of players now bringing this subscription-based service, which is, okay, you can have these collaborative robots and take them for a month and see how that goes. And the implementation is usually really fast, so capital expenditures go down quite a lot. And then if it works, you continue with that. Of course the operational costs might be a little bit higher than if you just did the whole investment upfront, but for a lot of the smaller companies, it's a pretty good solution that we see that is increasing quite a lot in the last couple of years. And in terms of how you bring that solution, the beginning on how you can prove that this has potential, we also see something sometimes called in industry simulation as a service, which is in this robotics as a service. Even before I bring you the robots, I can actually get data from you and run a simulation internally to see if this kind of solution would fit your business model. So we see different paths for this transformation that can, hopefully, impact not only big corporations but also help smaller companies to transform their facilities in the near future.
- I have to say that I like simulations but I don't trust simulations. Because the problem with simulations is that whatever you get in, and if the data is not right or conclusive enough, you don't get the right result out, you know? And it happens so many times that we try to work with simulations, so we build a few different sortation system and we tried to simulate how it's gonna, oh, how the boxes will move on the sortation. And everything worked perfectly. The moment you turn it on, and suddenly bam, something you never thought about suddenly hit and everything is falling apart in that. So my thinking about simulation is really you need to reach that through a digital twin. That's the way I'm looking at things. And I know what I'm saying here, it's a big deal.
- Quite aspirational still. I haven't seen any digital twin working 100%.
- So our method of digital twin is actually three steps, right? The first one is creating the right visibility. You need to start with that because a lot of the time you don't even have that visibility. You don't know what you don't know. So really creating a system that can show you everything that's in whatever environment you're trying to create digitally, show you everything that moves, everything that happens there in real time, that's phase number one. But only by that, you're only gonna create savings because now you know what you know, and it's not just based on some historical data, but come from here or there. If you talk about warehouses, it's gonna be WMS normally. So much information is lacking over there. You don't really see how people are moving around. You don't see how things are really happening. You only see, oh it's here. It was there, now it's here. You need that quantities, etc. The rest of the thing, you're guessing, and you become, everything is wrong at the end of the day because you don't guess it correctly, right? So that's step one, visibility. Step two is actually optimization. Try to optimize things based on what you see. So, okay, maybe first people optimize it, now let the machine optimize. There's so many better ways for machine to do it than us, looking at all the millions possibilities. And only the third step is actually the simulation and what-if scenarios that by reaching that level, you probably solved so many problems already with step one and step two, so now you reach to the, okay, let me introduce something new to that environment, how it's gonna be look at. And even that, that new thing, you cannot guess it because if you push a guessed data, it's not going to look right. You need to probably see it in somewhere else that it's working, and that taking some assumption and say, "Okay, in this environment, show me multiple ways that it's potentially gonna work." I agree with you that it's not there yet, but I think that a lot of simulation, you need to be super careful of what you feed it in with because otherwise you just get potential stuff that maybe not true.
- Yeah, I totally agree with that. And I would say that also from, maybe I'm getting too technical here, but simulation in this kind of, you know, simulation-as-a-service scenario, which is, like, if I'm a small corporation that maybe doesn't have access to those, like, big digital tools at this point, doesn't have a big team working on it, I think it's better than nothing. I think if you can do, of course, some stochastic simulation, which means that you're taking into consideration the variability. So you know you're not gonna get perfect answer, but at least it's a guide to what the system can behave like. 'Cause if not, you're going totally blind towards a new solution.
- As long as they can provide the data that you're asking for, which is,
- That's true.
- you know and I know, we all know that's the most difficult element, right,
- Getting the data right.
- just getting the data. Getting the data is the first place, and getting the right data and getting it cleaned or cleaning it, it's, like, this is a huge project by itself, right?
- We have a whole research line in the omnichannel supply chain lab, which is supply chain visibility. It's just about how to get the right data, how to get the single sources of truth. And we haven't seen any company solve this yet.
- As far as ROI goes, are you able to quantify for folks beyond a simulation, right, which, Erez, you say you have your doubts about, are you able to quantify for Maersk, for instance, like, when you implement these things and it costs us much upfront, this is what we're getting out of it?
- 100%. That's what we do in the proof of concept, right? When we're starting in a scale that is not too expensive to try, basically what we putting all our hypothesis and all our different thinking there and what is the expected result and what is not gonna make sense if it's a result. And that's, think of it as running a lab on a real environment. So that's, basically, what we do as a proof of concept. And what we ending up with is actually something that you say, technology that you say, "Okay, this is gonna take me 1.2 years to return. That technology gonna be 4.5 years to return." And now you start to be picky because you can't run all these projects and deploy all those things at once, so you say, "Why would I go on a four and a half years if I can go, like, I have so many projects that can go within less than two years? I'll start there. I'll reach that one. It's not that I don't care about this but let's park it for now." There is a lot, a lot, a lot of things that actually the return is quite short. And for 3PL like us, third party logistics provider, it's important to have relatively short ROI. The reasons for that is that it's not our business, it's not our goods. We're not running our own supply chain. It's someone else supply chain. And the contract land is anywhere, let's say, for a warehouse is normally between 3 years to 5 years, maybe 7 years, sometimes 10 years, but most of the time it's 3 to 5 years. Now, if your ROI is four and a half years and you have a contract for five years, why would you even do that? You don't know what will happen after that contract ends. Just to enjoy of that return for half a year, it doesn't make sense at all, right? So you do want to have a short ROI for what you do. It bring you to that need for flexibility. So if something change, if your customer, this customer leave and that customer come, and it's slightly different business, you can't just design for something and that's it 'cause otherwise you're stuck with a lot of things that very difficult for you to move. So you want that flexibility of how you do things that it can take the next customer, it can take the next change of behaviors, of consumers. That helps to convince.
- Are there so many opportunities for improvement that you could put them up on a dart board and throw a dart and say that any of these are gonna help us next? Or-
- Oh there is.
- are things so prioritized because we know this one, two or three things are gonna have that return that's short and sweet?
- What we have been seeing lately is that that's actually one of the main pain points, that there are so many solutions out there that actually companies have issues keeping up pace with all those advancements. 'Cause, like, okay, how do I look at all these environment in terms of different warehouse solutions, different warehouse providers, and how do I prioritize, as you were saying. Like, how do I have a team looking at all these and actually bringing the solutions that are gonna work? Erez mentioned the proof-of-concept approach that Maersk follows, which I think is pretty good in terms of having a standardized method to go through this evaluation of solutions, but many companies are struggling with this because of the number of suppliers in recent years has been increasing a lot. And one of the main reasons for that is because companies are looking for more tailored automation too. The amount of companies out there that have specific needs is what has brought all these new suppliers into the game. And that also correlates with something that Erez was mentioning, which is okay, at some point, you're gonna have 3, 4, 5, 10, 20 different technologies that you're trying to implement at the same time, and that brings new challenges. And during the roundtable, a lot of the participants, the roundtable that we talk about in the white paper, which was held last year by MIT CTL and hosted by Maersk, so all the executives were actually saying that interoperability was one of the main issues. 'Cause when you have all these different solutions and you have to integrate them all together, you have different platforms, different protocols, you have different softwares that you're trying to put together. And that's a main pain point for many companies. And actually, a couple of weeks ago we had a big CPG, one of the largest in the US, coming to CTL, and they were actually saying that this was their number one issue in their global warehouse network nowadays. And what they're looking at right now is to build their own interface to try to integrate all these different solutions together and also looking forward 5 to 10 years 'cause they think, okay, more solutions are gonna keep coming, so we need to have something that is flexible and that we can just plug in and out as we need. So definitely a really big, big challenge in terms of having this broad range of solutions to pick from.
- Solution wise, absolutely there's way too many, maybe not too many, way a lot of solutions out there, but I think also you wanted to know about problems to solve, and we still have a lot of that, so. But we're not just, okay, let's go for this one first, let's go for that, gambling on that, We're, basically, what will be the impact of solving this problem. So we do prioritizing it, and we do prioritize based on the problem importance but also based on an ROI of course as I mentioned before. It is important to stay within certain criterias on that. And also, how does it impact the before or after of the supply chain? 'Cause, again, warehouses are important elements of something much bigger, and you always have to remember that bigger thing. 'Cause if you just isolate, solve stuff here without thinking the before or after, you end up with a different problem somewhere else, right? So you do need that connectivity of the whole supply chain.
- And I think in the white paper, we mentioned something about that multi-criteria analysis that Maersk follows when analyzing or evaluating a technology 'cause you guys consider many things like safety, throughput improvement and improvements also in cost efficiency. So many different aspects that you have to bring together to actually evaluate correctly.
- So what kind of role does sustainability play in the warehouse of the future?
- I think it's definitely an important, large role, you know? Because at the end of the day, the world is going into that direction. There are certain region that is faster than others. I'm not gonna mention names here. I still want to be welcome in many different places, but.
- By the time this airs, it might be a different list of people.
- Exactly. So if you're thinking about airing it in 10 years, you're right. But no seriously, at the end of the day, companies are trying, and Maersk itself also trying to be, like, a zero-net emission by 2040, other trying to do it in slightly different pace and different time. But this is an important roles to play when you're looking at the end-to-end supply chain. You have to become sustainable also for the warehouse. And at the end of the day, as I mentioned before, the sustainability can come up with savings. 'Cause normally when you reduce your pollutions, this means that also, in a way, you reduce either your energies or your total moves. You reduce something else as well that should be considered together when you're trying to do that in order to ensure that, you know, it's much easier to get the buy-in to run those sustainable. And another important point is, of course, the final consumer. Whoever buy the goods, if they're demanding goods to be arriving to them and shipped to them and created for them in a much more sustainable way, you need the warehouse to be sustainable as well.
- So one quick question, and this is interesting 'cause do you guys at Maersk have this perspective? Are you seeing willingness to pay for that in your customers?
- I would say we have about 5% of our customers that are willing to pay more for that. There's probably another, I dunno what, 15% or slightly more than that of people that they wanna be not the frontier there, but they're willing to follow very fast etc. But still a lot of the majority are still either on the fence or doing it because they're being forced. Again, depend where in the world, right? It really depends. Some countries, people just, "Sure, let's do it because it's the right thing to do." In other places, "No, I'm not gonna pay more because of this, you know? Find me another way." But I think it's also good to do that. Sustainability needs to be sustainable, right? You can't just ask people to put more and more money without getting something benefit out of that. And I think it's good that they're pushing us. It's like, "Sure you wanna charge so much more because it's sustainable. Yeah, good luck on that. Find me a way that it can be sustainable and still cost neutral or even cost reduction. Can you do that?" I believe that, yes. At the end of the day, maybe not for everything immediately, but, you know, I think there's so many things that you can actually do, so why not start with those?
- Well, in the research project that we did last year with Maersk and a couple of students from MIT, we actually proved that many of the solutions, the green solutions that you can bring to the warehouse nowadays, they have really, really short ROIs. So you can have return on investment for green energy generation, which is one of the aspects that you can adopt, like, right away. 'Cause, for example, in places where solar panels can produce a lot of energy, you can go to power purchase agreements, which is a type of agreement that removes the capital expenditure of the company and just makes some other player implement those solar panels and then sell you the energy, like, later on. So you can remove the initial investment, and you can just get cheaper energy right away, which brings an economic improvement and, of course, also a sustainability improvement at the same time. So that's one of the things that we saw in that research. And then, of course, other ways of bringing sustainability into the warehouse, the discussion that we had at the beginning of the podcast, retrofitting existing facilities versus building a new facilities. 'Cause, of course, when you build a new facility, there are a lot of embodied carbon emissions in the infrastructure, the new automation. So the idea of retrofitting existing facilities is also important, and there are a lot of low-hanging fruits in that aspect. And then, of course, new, more efficient technologies like electric forklifts. Of course there are some hydrogen technologies now out there. I don't know if, I think Maersk is also piloting or trying some of those. I don't know about the success of many of those, but many different things that can bring a more sustainable warehouse.
- And I think you can also do something even simpler. You go to your electric provider and say, "I want to buy only sustainable energy from you." 'Cause, for example, we opened in the last few years, like, nine different warehouses in Savannah area in Georgia, and we wanted to put on all of them solar panels. But the answer was, "Sorry, you cannot do that." And we asked why. They say, "Oh there is an airport nearby, and, basically, solar panel can actually blind the pilots when they're trying to to land, so it's a risk." All right, we didn't think about that when we asked for that. So they say no and we cannot do that over there. But then you can still go to the electric company and say, "Hey, I wanna buy a sustainable energy from you." And that, they can put those things doing those things somewhere else and still sell you the right thing, so.
- Yeah, they offer that to individuals, to residents through municipalities now.
- And I don't think it's so difficult to make it sustainable, but again, materials, those type of things of all buildings, it's probably gonna take a while.
- There's a tricky aspect on that, which is the implications of ownership sometimes in the facility. 'Cause because of how the warehouse industry is right now, you have, of course, 3PLs involved, but you also have real estate companies that sometimes own the land and also the infrastructure. So in terms of bringing a lot of these sustainable solutions that sometime required a few years to to pay back, I think companies need to get together and actually start talking about some contract terms that can benefit the implementation of a lot of these solutions. 'Cause even if you have a lease for the next few years as an operator, and you see okay, maybe the solar panels or whatsoever takes a ROI of five or six years, but it still might a good investment. So you might just wanna go to your partner in that business and say, "Okay, maybe we share the cost and we also share the gains." So I think the implications of ownership is something tricky that we have also seen from the research perspective. And yeah, hopefully we'll see more and more companies talking to each other to establish these contract terms that help bringing more sustainable solutions to the warehouse.
- The good thing is that there are few of the larger real estate owners. The good thing is that there are few of the larger real estate owners are doing it already. Of course not all of them. And it's very fragmented business 'cause when you pick a location, you don't pick just based on who is the owner, you need that specific location. It could be, like, a mom and pop owner, and they probably don't have any interest to do that unless you're doing it, and you remove it at the end of the contract, which now becomes suddenly something you don't want to do it. But yeah, that direction is already in motion.
- So where does the research go next beyond your paper? What areas of this topic are yet to be explored?
- So at the omnichannel supply chain lab right now we have three research lines. One of them is actually related to technology itself because of these rising different solutions and also the huge vulnerabilities that a lot of these technologies are bringing, and let me explain myself. Back in the days, most of the technology in a warehouse were closed systems. So you have a lot of these solutions running in softwares that were on a Windows operating system. Nowadays, you have, first of all, a lot of these technologies running on Android, and also a lot of these technologies having connections with the cloud. So you have an open system, where a lot of stakeholders might have interest, and a lot of your data might be stored somewhere that is shared between you and many other clients. That happens, for example, when you have cobots. A lot of the collaborative robots, the way they run is based on a central AI system that is in the cloud 'cause it required so much computer power that it's really hard to actually make it on a local server. So that brings a lot of vulnerabilities to the systems. So one of the research lines that we have right now is looking at all these potential disruptions that can happen in terms of cyber attacks or even an unintentional disruptions because of the transformation to more highly-automated warehouses. Go with the floodings in California, if you have a facility that mainly runs on electricity and you have a grid power outage, you need something to keep operating. 'Cause at the end of the day, I mean, that flexibility of having humans at the warehouse, when you're going into more and more automation, you lose it, as we were mentioning at the beginning. So this technology transformation comes with a lot of downsides that research also has to look at. So that's one. The other one is robotics as a service. I think we also talked a little bit about this new business model, a subscription-based model that we believe can bring benefits to the supply chain. So we are looking at what aspects of the supply chain, not just the warehouse, this type of business model can benefit the most. And the third one, and I like this one a lot, is what we call optionality. And this term came actually from the VP of supply chain of one of the largest retailers in the US a few weeks ago. And he was sharing this need of coming up with a warehouse of the future that is able to adapt to whatever it comes. Different unit loads, but also big market changes, big disruptions, how do we create, how do we design a facility from scratch that is able to adapt to different cargos, to just adapt to volatility, anything that can happen. So we believe that idea is really powerful. We have been exploring it for many months in the past, but I think this term optionality is actually something cool that is gonna stick. So yeah, at this point, vulnerabilities in highly-automated warehouses, robotics as a service and optionality are the three research lines that we have in the warehouse of the future.
- And Erez, what did Miguel forget?
- Oh, they're doing many more things for sure.
- There's so many things you wanna do. So those are great topics. And there's so many deep dives that you can do in each of the elements. For example, Miguel was talking before about so many different solutions, so how do you choose? That could be a great topic to, like, what is actually, how to choose the right technology that fits your need. But I think something much bigger than that is actually is how the role of the warehouse in the big end-to-end supply chain is playing and how to improve that. So how can you make it much smoother? All the changes that he was talking about, the largest retailer, etc. are talking about is not only within the warehouse, is how do you actually become, so let's call it elastic, that you can change things and adopt new ways to work within the warehouse based on, you know, a problem that happened in the Red Sea, for example. So can that and should it be connected together? I believe that, yes, you know, there is a big deal on where you're working, how you're working, what are you doing here and there based on really the whole flow of end-to-end, and what is the end goal, right? What do you do? Why are you doing that? In my mind is at the end of the day, to reduce the amount of stocks that you have because that's way too much waste there today. And to improve the service level that you bring to the end customer. Can you do it together? I believe that, yes. But it requires a connection between everything and to work in such a smooth way. And that's a lot of research requires there.
- And do you think that is gonna be the digital twin what's gonna help with this, you know, end-to-end vision of the supply chain?
- Maybe many, many different digital twin and some control tower on top of it. 'Cause I don't think you can simulate the whole thing. It's such a complex thing, I don't know if we have the right power today. Maybe one day but there is so many things that you can do way before that, you know, with just the visibility of optimization levels that we talked about, and later, if you need simulation and digital twin really, okay, you bring it to this next step.
- So people often describe AI and automation as exciting and terrifying at the same time. How will these new technologies help warehouse workers do their jobs more effectively and help companies be more productive at the same time?
- Yeah, so I can understand why people are terrifying from AI, but at the end of the day, I see it as a supportive tool, you know? You can also be terrified many years ago from Excel. "Oh, it's gonna," you know, "It's so difficult, it's so complicated," but-
- To be fair, I'm still a little terrified of Excel.
- We all are, you know? There's so many functions there that you don't even know that exist. But I think the beauty of AI and the machine learning around it definitely can help. Let me give you an interesting example. Our continuous improvement team came to us few years back and say, "Hey, we are trying to improve the time it's take to manually unload containers. Can you help us?" Like, "Okay. Why do you need us for that? It sounds like a very easy problem to solve." And they said, "No, you'll see. It's not so easy." I'm like, "Okay, sure." So we went to some of our deconsolidation centers, those locations I was, transload I was talking about, and we looked into that. Now, the number of cartons inside a container can go from few hundreds to 15,000. So you had a huge range of number of cartons. A lot of them are coming floor loaded, some of them you can palletize so it's easy with a forklift. It's very simple to do that but a lot of people trying to utilize the container to maximum possible, so they're floor loading it. Now, in a deconsolidation service, you're, basically, splitting it per destination per instruction from the customer. So they tell you, "Okay, this queue take 150 cartons and move them to this DC, and about 22 cartons go to that DC." And assume you have 20 DCs now, that takes a lot of energy from the people that doing that to just, "Okay, this is that and this is this and put it on a cart and push it." We're talking about manual environment right now, right, which still exists out there. It's not all automated. So we started originally by using an Excel. We say, "Okay, let's try to put some assumption and create something." We went so off. At the same time we ask also the supervisor, "What do you think this container takes?" So the guy says, "I feel six hours." We called another supervisor, "What do you think it's gonna take?" And he say, "Oh, this is about nine and a half hours." I'm like, "Okay, that's a huge difference." Call the third guy, let's see if they're gonna bring us in between. Threw us even more off. He's like, "Oh, this is 11 hours. I'm kind of positive it's gonna take that much." Really it's like there's nothing out there that give you the right insight into that. So Excel didn't work. The knowledge of the people, the tribal knowledge didn't work. We say, "Okay, what's the next labor management system? Let's go with that." Now, the problem with LMS is that if you don't have any input to scan or to do something, you have no clue what's going on. The system have no clue. So we said, "All right, there's no scanning going on. It's all manual." So there's nothing robotics to count it for us or to do anything. You scan only one cart at a time, and you don't really know how many cartons by the scan, but it's only on a paper. We put tablets next to the door of the containers, basically checking in, checking out. I said, "Okay, just to know how many people did the work? Is it one, is it two, is it three? When did they actually been there?" So we failed miserably. Nothing. We couldn't get any knowledge out of that. It was, like, so off. Then we said, "Okay, let's talk about computer vision and AI here. Let's understand how can we solve it in a different way." So we actually installed cameras in each of the doors, and those cameras learned, keep looking at how many people are there, what's the depth, realize what's the depth already completed into the container. How do they do that? Do they do it manually? Do they do it with a forklift? Do they do it with a cart? So it started to learn all these elements, bring it all together, and the AI and the machine learning behind the scene, after seeing tens of thousands of containers, started to give us a much better prediction on how long it would take. So we had slightly above 80% of the accuracy there. I don't think we will ever go anywhere above that, you know? 'Cause there's still so many unknowns that you don't know. You know, the guy didn't feel well, or the girl didn't feel well. Last night they ate too much.
- But 0 to 80 is not bad.
- Yeah. From 9 to 6 to 11, suddenly you come to an 80 something percent accuracy, now you can incentivize the people, and say, "Based on 80%, I'm willing to start giving you incentive to do it few minutes less than that." Not only that, you now can start synchronize the work between the warehouse and the yard that connected to that, and bring, get ready the next container about 10 minutes before it's really happening. Before you never knew where is that 10 minutes coming. So AI, in one hand, scared the people, "Oh, why do you watching me? Why are you doing that?" But we're not watching you as Erez or whatever, or Dan or whoever it's the person, we're watching the work being done. We're not putting names to the people there. So actually it's collaborating with them, helping them to earn more money in one hand, helping our whole operation to actually flow in a much better way there, and that's, I believe it's a good example on how you can actually play with AI and machine learning and bring them in to support people in decisions.
- And I think, just to compliment on that, the idea of human/machine collaboration that Erez was mentioning, I think is where AI has most potential in the warehouse. We talk about some of these solutions in the white paper, but, for example, exosuits is something that is pretty, I mean, has been out there for many years. It's a wearable device that usually support workers to just heavy items or to just perform any kind of manual task. And AI actually brings what's called a flexible and adaptable exosuit that is able to adapt based on your own movements. So if I'm just standing and doing nothing, it's not gonna be actually performing any kind of task, but if it feels that I'm moving, I'm lifting something or I'm actually just pushing a cart, it's actually gonna support that specific movement based on my muscle position and how I'm actually moving at that specific moment. So that's just one example. But in terms of human/machine collaboration, a lot of AI applications there, collaborative robots, it's something, it's another big solution that actually takes a lot from AI. 'Cause, for example, in terms of predictive maintenance for the robots, in terms of how the robots can avoid collision, they learn from each other, they learn where they are going, and then something cool that a tech provider actually shared with us the other day is that when you have this collaboration between humans and robots, you can even do the robots learn about the humans. So when you have, for example, picking robots that collaborate with just human pickers, then the robots can learn, "Oh, this specific person actually takes a little bit longer on doing this task 'cause maybe he's a little bit older, it's a little bit harder for them, so I'm gonna, as a robot, I can adjust my timing, my movement to go maybe a little bit slower with that person, or if I'm maybe working at this point with someone who's a little bit faster, I can adjust to that too." So that reinforcement learning of this kind of tools is only possible thanks to AI. So yeah, a lot of possibilities. I'm pretty sure that we'll see more and more coming in the next year 'cause this field has a lot of potential.
- Well, our guests today have been Erez Agmoni, global head of innovation logistics and services at Maersk, and Miguel Rodriguez Garcia, postdoctoral associate here at the MIT Center for Transportation and Logistics. They've just completed a white paper exploring the warehouse of the future. Thank you guys both so much for spending some time with us. I've really enjoyed that conversation. It's good to be in person, in front of people talking about this stuff.
- Thank you for having us.
- Thank you so much for having us. It was a pleasure.
- Thank you for listening to this episode of MIT Supply Chain Frontiers presented by the MIT Center for Transportation and Logistics. To check out other episodes of MIT Supply Chain Frontiers, visit ctl.mit.edu/podcasts. And for more on the center's research, outreach and education initiatives, make sure to visit us at ctl.mit.edu. Until next time.